sludge treatment equipment paramter:
Models | Basket diameter (mm) | Rotation rate of basket (r/min) | Relative centrifugal force | Motor power(kw) | Productively M3/h | Weight(kg) | Dimension (L*W*H)mm |
LW250x900 | 250 | 5400 | 4000 | 11 | 1-5 | 1050 | 1800*1200*600 |
LW360x1200 | 360 | 1200 | 4200 | 15 | 3-12 | 2100 | 2600*1580*1040 |
LW360x1500 | 360 | 4200 | 3550 | 22 | 3-14 | 2600 | 2900*1600*1040 |
LW420x1750 | 420 | 4000 | 3750 | 37/45 | 6-30 | 3500 | 3120*1580*1070 |
LW420x2100 | 420 | 4000 | 3750 | 45 | 6-35 | 4100 | 3450*1580*1070 |
LW500x2000 | 500 | 3800 | 4000 | 45/55 | 10-40 | 6500 | 3600*2300*1400 |
LW500x2500 | 500 | 3800 | 4000 | 55/75 | 12-45 | 7200 | 4100*2300*1400 |
LW550x1900 | 550 | 3200 | 3154 | 45/55 | 13-50 | 4600 | 3400*1810*1110 |
LW550x2400 | 550 | 3200 | 3154 | 55/75 | 13-55 | 5600 | 3900*1810*1110 |
LW650x2000 | 650 | 2650 | 2500 | 55/75 | 15-65 | 7100 | 4000*2300*1400 |
Operating principle[edit]
The operating principle of a decanter centrifuge is based on separation via buoyancy. Naturally, a component with a higher density would fall to the bottom of a mixture, while the less dense component would be suspended above it. A decanter centrifuge increases the rate of settling through the use of continuous rotation, producing a force equivalent to between 1000 to 4000 G's. This reduces the settling time of the components by a large magnitude, whereby mixtures previously having to take hours to settle can be settled in a matter of seconds using a decanter centrifuge. This form of separation enables more rapid and controllable results.
Range of applications[edit]
The main application of decanter centrifuges is to separate large amounts of solids from liquids on a continuous basis. They are also used to wash and dry various solids in industry, such as polystyrene beads, clarify liquids and concentrate solids. Table 1.0 displays various examples of the utilisation of decanter centrifuges in various industries.Table 1.0: Industries with corresponding examples that use decanter centrifugesIndustryExamplesFood processingPetrochemical/oilIndustrial and biological wastewater treatmentFish processingChemicalMineral processingOrganic chemical industryPolymer IndustryInorganic chemical industry
Edible animal fat Plant oils such as olive oil and vegetable oil Wine (clarification) Fruit juice Soy protein Dairy (recovery of lactose, whey fines and cheese fines) Coffee and tea |
Refining De-watering Oil well drilling Lubricating oil additives Waste oil stream recycling |
Municipal wastewater Cleaning of wash water |
Fish meal Fish oil |
Herbal medicines Chemical extraction |
Bentonite and titanium dioxide manufacturers Kaolin clay and calcium carbonate processing |
Organic intermediate and end products |
Thermoplastics for example PVC, synthetic rubber and fibres |
Bleaching agents Acids Silica products Fertilisers |
Advantages and limitations over competitive processes[edit]
Generally the decanter centrifuge has more advantages than disadvantages; however there are some limitations when compared to other processes.
Advantages:
Decanter centrifuges have a clean appearance and have little to no odour problems.
Not only is the device easy to install and fast at starting up and shutting down, but also only requires a small area for operation compared to other competitive processes.
The decanter centrifuge is versatile as different lengths of the cylindrical bowl section and the cone angle can be selected for different applications. Also the system can be pre-programmed with various design curves to predict the sludge type, while some competitive processes, such as a belt filter press, cannot change the belt type to operate for different sludge types.[1]Its versatility allows the machine to have various functions such as operating for thickening or dewatering.
The machine can operate with a higher throughput capacity than smaller machines.[2] This also reduces the number of units required.
The device is simple to optimise and operate as it has few major variables and reliable feedback information.[1]
The decanter centrifuge has reduced labour costs compared to other processes, as it requires low continuous maintenance and operator attention.
Compared to some competitive process such as the belt filter process, the decanter centrifuge has more process flexibility and higher levels of performance.
Limitations:
The decanter centrifuge cannot separate biological solids with very small density differences, such as cells and viruses.[2] A competitive process that is capable of separating these difficult-to-separate solids is the tubular-bowl centrifuge.
The machine can be very noisy and can cause vibration.
The device has a high-energy consumption due to high G-forces.
The decanter centrifuge has high equipment capital costs. Hard surfacing and abrasion protection materials are required for the scroll to reduce wear and therefore reduce the maintenance of the scroll wear.
Designs available[edit]
The main types of decanter centrifuges are the vertical orientation, horizontal orientation and Conveyor/Scroll.
In vertical decanter centrifuges the rotating assembly is mounted vertically with its weight supported by a single bearing at the bottom or suspended from the top.[2] The gearbox and bowl are suspended from the drive head, which is connected to the frame.[2]The vertical decanter allows for high temperature and/or high-pressure operation due to the orientation and the rotational seals provided at one end. However, this makes the device more expensive than the horizontal decanter centrifuge, which is non-pressurised and open.[3] The advantage of the vertical machine over the horizontal machine is that the noise emitted during production is much lower due to less vibration.[3]
In horizontal decanter centrifuges, as shown in figure 1, the rotating assembly is mounted horizontally with bearings on each end to a rigid frame, which provides a good sealing surface for high-pressure applications.[2] The feed enters through one end of the bearings, while the gearbox is attached to the other end and is operated below critical speed.[2] Capacities range up to 40,000 pounds (18,000 kg) of solids per hour with liquid feed rates of up to 300 US gallons (1.1 m3) per minute.[4] The horizontal machine is arranged in a way that slurry can be introduced at the centre of a rotating horizontal cylindrical bowl.[4] The scroll discharge screw forces the solids to one end of the bowl as it is collected on the walls. This orientation is the most common design implemented in industry.
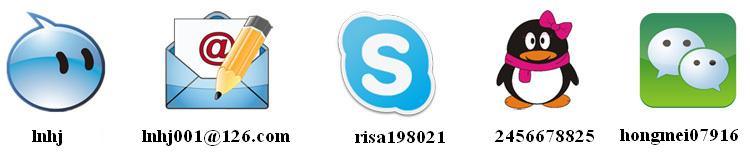